Multiscale modeling of catalytic coated monolith reactors for emission reduction
- contact:
- funding:
German Research Foundation (DFG)
Project description
The purification of industrial waste gases from pollutants and greenhouse gases is mainly performed using catalytic coated monolith reactors. The reaction at the catalytically active center is strongly influenced by heat and species transport limitations. Therefore, the optimization of the monolith geometry (e.g. channel size and shape) and the morphology of the catalyst coating (e.g. porosity profile, pore diameter, location of catalytically active sites) holds great potential to improve the performance of reactors for exhaust gas control.
The spatially resolved modeling of the system can contribute significantly to a better understanding of the process and is a necessary step on the way to computer-aided reactor and catalyst development. Within these reactors, however, processes take place on different size and time scales, which makes their modeling challenging.
In order to better understand the complex interaction of these processes, a hierarchical multiscale model for the simulation of technical catalysts and associated reactors for emission reduction is being developed as part of the project, which covers the reactor, macropore and mesopore scales. Separate, high-resolution simulations of representative sections and time periods are used to derive computationally efficient surrogate models, which are then used to couple the different scales (see Figure 1).
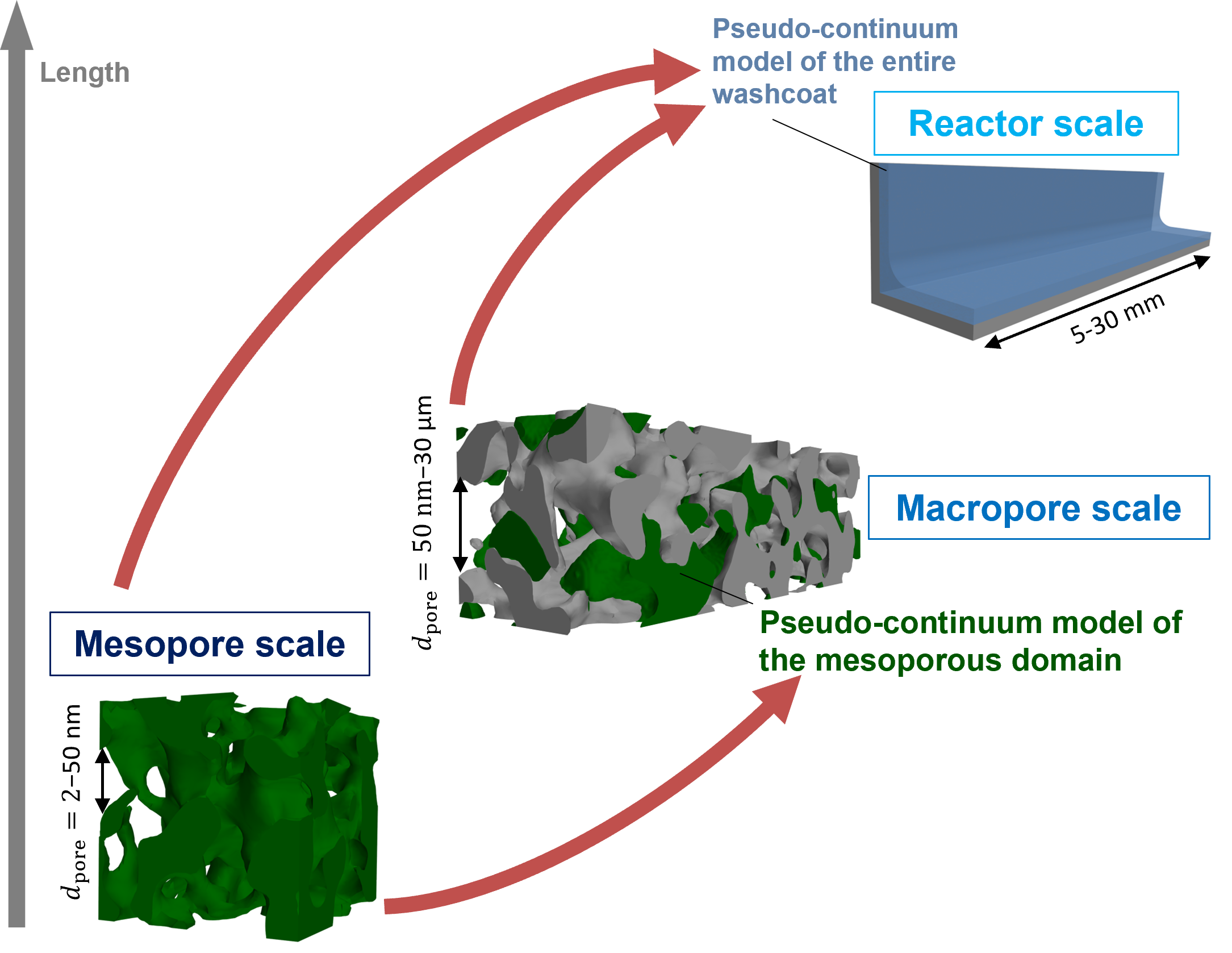
Ultimately, this will enable the calculation of the behavior of reactors and technical catalysts in detail and advance in order to support the development of new, sustainable solutions. The research project is part of the Collaborative Research Center 1441 TrackAct and is funded by the German Research Foundation.